MET RC BAJA
Construction
The RC Baja car will be constructed part by part. The sub frames will be the first parts to be constructed. This is because these parts are the most important parts to get right so that all the other parts that will mounted off them will be correct as well. The suspension and steering will be constructed in three different assemblies. The front suspension is the biggest assembly because it contains the greatest number of parts. The front suspension must account for the steering while the rear suspension just must account for the rear solid axle. All the 3D printing will be completed by Garrett Bailey and all the machined parts will be completed in house at the CWU Hogue Machining lab. The control arms, and front sub frame will be machined aluminum. The rear sub frame and front shock tower will be outsourced via Send Cut Send. The rest of the components will be 3D printed.
Up until the beginning of February, roughly 50% of the parts have been constructed on the suspension and steering side of the project. The rear sub frame flat pattern was received as a aluminum flat pattern and by making a fixture to hold the part in a vice, bend relief grooves were cut using a Bridgeport and a finger press was used to bend it into its final shape. The front sub frame was milled completely from stock aluminum on the Bridgeport and finished off with tapping the necessary holes. The front control arms were laser cut roughly and then machined to final finish on the Bridgeport. Trailing arms were programmed and ran on the CNC mill.
As of the 7th week of the winter quarter, 100% of the parts that were designed were completely constructed and 100% of the purchased parts were at least ordered. After the trailing arms were finished, the lower subframe mounts, axle mounts, and radius arm mounts were constructed by 3D printing using Garrett Bailey's 3D printed. Originally these parts were a little concerning to be completed by 3D printing but after they were ran, the quality of the parts exceeded the expectations and should work perfectly. In the remainder of the winter quarter, the car will be final assembled and must meet the requirement of driving forward, backward, and steer under its own power. The students are confident that this requirement will not be an issue to achieve.

Figure 3.1 shows the steps taken to construct the rear sub frame. The subframe was modeled then water jet cut from aluminum by Send-Cut-Send. The flat pattern, as shown in the top left, is what was delivered to the students. A fixture was first machined with matching holes too the flat pattern so that it could be fastened securely in a vice in order to cut relief grooves where the bends were made. After the reliefs were cut on the Bridgeport, the frame was bent into its final shape by using a finger break.
Figure 3.1

Figure 3.2
Figure 3.2 displays Garrett Bailey on the Bridgeport machining the front sub frame. Garrett had a introduction to running a mill in his freshmen year but never had another opportunity to fully learn how to use it to produce a part. The rear sub frame, shown previously, was the first part Garrett ran on the Bridgeport but only for simple groove cutting. The front sub frame was the first major part that Garrett produced completely on the Bridgeport.

Figure 3.3
Figure 3.3 is a time lapse of Garrett Bailey making some stock pieces that will be ran in a CNC program. It is crucial for stock to be prepped properly so that cuts only what it should. This stock is the beginning of the rear trailing arms.

To the left is Garrett Bailey running the CNC mill for the first time. Prior to this opportunity, Garrett has not had the chance to run a CNC let alone set the whole program up on his own. The rear trailing arms were ran on the CNC with only minor finishing operations completed on a Bridgeport.
Figure 3.4

In Figure 3.5 are the trailing arms that were ran in the CNC mill. These parts weren't only Garrett's first ever CNC parts but they also were ran on only one set up with multiple operations. Not seen in the figure, but the bottom contour used a hem stitching operation so that the part only needed one set up.
Figure 3.5

Figure 3.6 is a time-lapse of the CNC mill performing some of the machining for the Baja car. The CNC used for this project is a MIlltronics and most of the operations are carried out with an endmill. The parts were typically designed in SolidWorks but then converted into Fusion360 to write the programing.
Figure 3.6

This Figure 3.7 is a very excited image. This is the first attempt of assembling the front suspension. Test fitting was a very important step in construction because all of the parts are designed and assembled in 3D modeling but after manufacturing in the real world, they may not fit completely as intended. Luckily, this first assembly was a success and only required some light filling and polishing to get the correct fit.
Figure 3.7
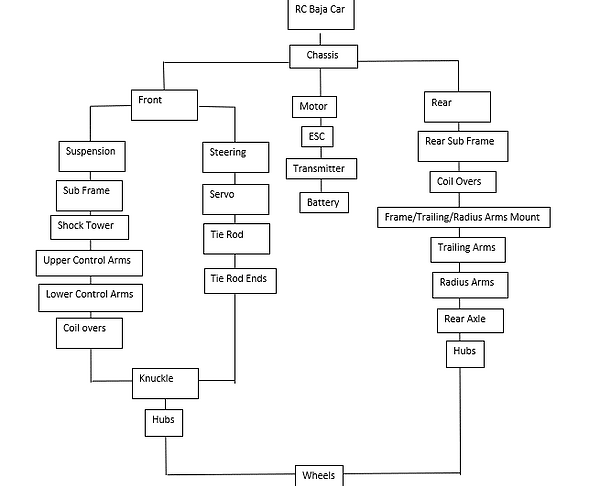